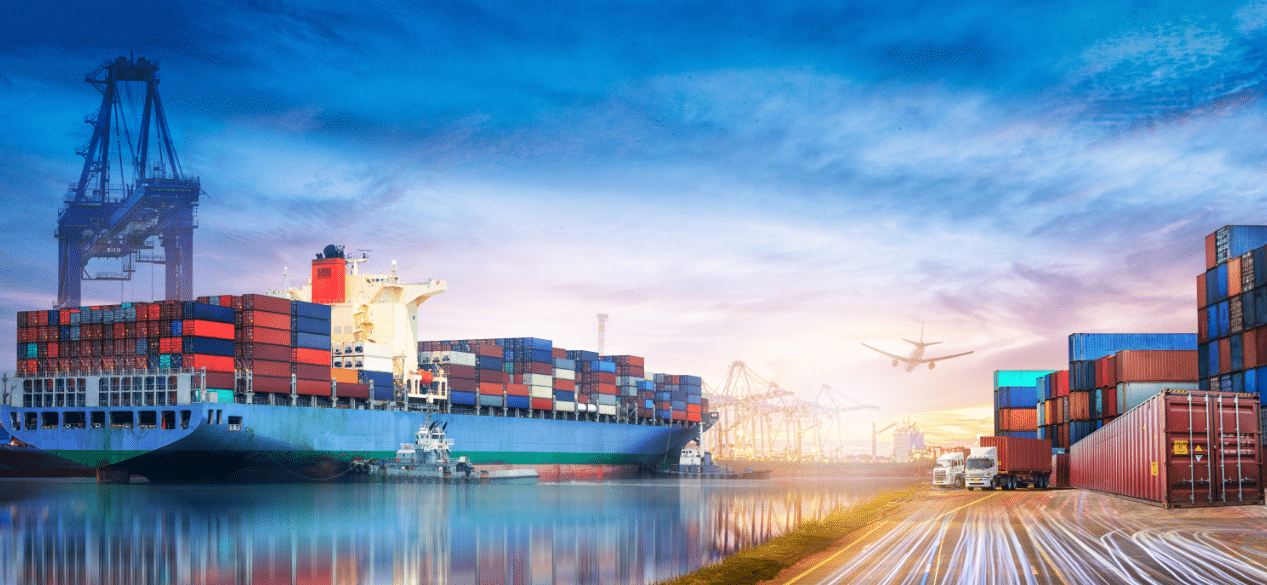
Vertical integration allows battery manufacturers to control every stage, ensuring the quality and consistency of their products.
As supply chain issues have become apparent in recent years, more battery retailers are partnering with domestic battery manufacturers that have a vertically integrated supply chain.
Domestic vertical integration offers a substantial competitive edge and reinforces the value of the sustainable lead battery circular economy.
Domestic Versus Imported
There are several factors to consider when deciding between a domestic and an imported battery manufacturer. Each option has its advantages and considerations.
Imported batteries may initially seem attractive with lower acquisition costs. But the trade-off involves extended lead times of 60-180 days. Challenges related to that lengthy lead time include fluctuating inventory costs and potential hiccups in the importing process.
Because of the prolonged transit time, imported batteries often need to be boosted before being sold. Domestic battery manufacturing supplies a fresh product with a shorter lead time to delivery. Category management services, marketing support and insights, technical support, and quick response times are other advantages of working with a domestic battery manufacturing partner.
Domestic battery manufacturing also employs a large workforce, contributing to the U.S. economy. The lead battery industry contributes almost $33 billion to the national economy and supports more than 121,00 U.S. jobs. Battery manufacturers are highly committed to improving the communities where they work and live. They volunteer and support local charities, and partner with colleges and universities for research and job opportunities.
The Advantages of Vertical Integration
Vertical integration in battery manufacturing is crucial for several reasons. Companies can ensure the quality and consistency of their products by having control over every stage of the process. This is vital to building trust with customers.
Vertical integration brings cost advantages by streamlining processes, reducing dependencies and providing a greater understanding of cost drivers. Visibility allows manufacturers to offer batteries at a competitive rate while protecting against supply chain disruptions and additional charges associated with long lead times.
Importing batteries prolongs the customer’s wait time and brings additional potential costs. With the additional labor, time and energy usage, any necessary boosting adds another $2-$3 cost per battery.
Agility with Domestic Vertical Integration
Vertically integrated domestic battery manufacturers can control various aspects of production and decision-making, allowing companies greater control of their operations. Goals are better aligned with long-term strategies, when independent from external influences such as supply chain disruptions.
This autonomy allows for a deeper understanding of the domestic market and facilitates greater market readiness. Vertical integration makes domestic manufacturers more agile and better able to respond and adapt more quickly to market trends. Partnering with these manufacturers helps retailers to make timely adjustments to meet consumer needs, increasing their customers’ satisfaction.
Addressing the Environmental Impact
Partnering with domestic battery manufacturers has a lower overall environmental impact. Importing batteries requires more time and energy to transport products into the United States due to the increased distance from the manufacturer to the retailer.
Recycling is another important aspect of domestic battery manufacturing. Nearly 100 percent of spent lead batteries in the U.S. are recycled. This keeps more than 160 million lead batteries out of landfills.
U.S. battery manufacturers source about 83 percent of the needed lead from domestic lead battery recycling. As a result, a new lead battery produced in the U.S. is typically comprised of more than 80 percent recycled raw materials. The robust circular economy of the lead battery industry is a model for other battery chemistries working toward the sustainability of their manufacturing, distribution and recycling processes.
Still, we can further strengthen our lead battery recycling supply chains. Some lead batteries are sent outside of North America for processing and remanufacturing. In many cases, they are then imported as finished batteries from foreign manufacturers.
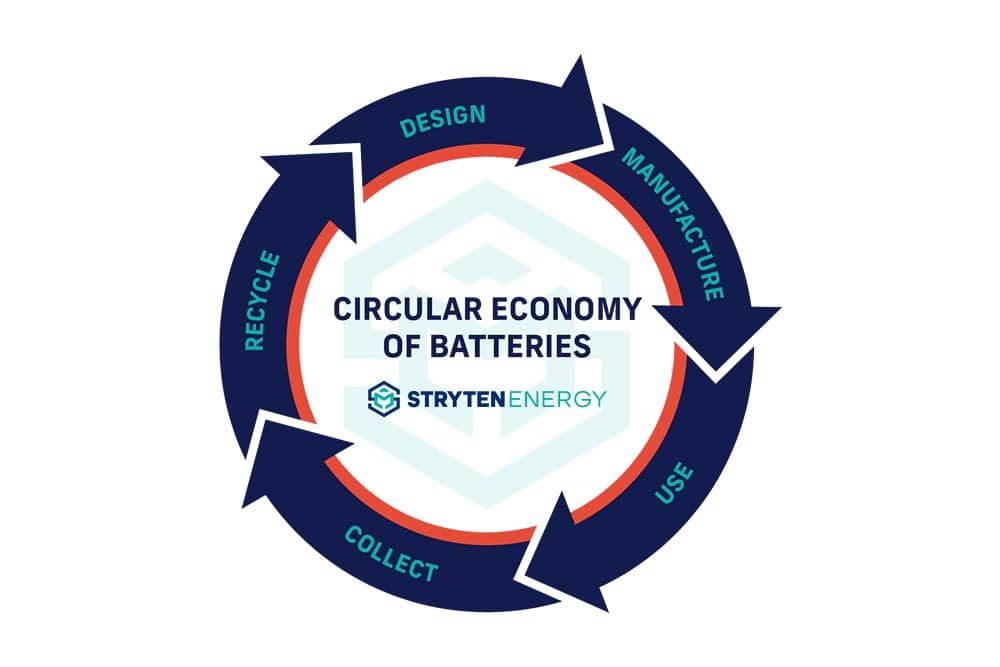
There are also concerns about how materials are handled overseas. U.S. battery manufacturing and recycling industries have extremely comprehensive worker safety and environmental controls, protecting people and the environment. Today, the U.S. government and private industry are working together to establish reliable domestic manufacturing and supply chains for new battery chemistries that avoid materials and finished products sourced from countries of concern or that violate forced labor laws.
By partnering with vertically integrated domestic battery manufacturers, retailers can help reduce reliance on foreign sources for energy storage, which provides the U.S. greater energy security and independence.
Bill Nonnamaker, Vice President of Sales, Transportation